We started with a simple idea.
How to keep the lug nuts from falling off a vehicle. Simple yet ingenious design reduces the risk of wheel loss by securing adjacent wheel nuts together and minimizing their ability to rotate.
Zafety Lug Lock® is a wheel nut retainer not just a wheel nut indicator.
Tafcan Consulting Ltd. – with Zafety Lug Lock®
Working to make vehicles and roads safer one wheel at a time and peace of mind to owners, operators and the public.
Ifor (Taffy) Davies, President of Tafcan Consulting Ltd., is the inventor and manufacturer of Zafety Lug Locks®.
Taffy felt that it was important to focus on the largest vehicles first, as the accidents caused are costlier with damage, potential fines, lawsuits and are often tragic with victim injuries and fatalities. Other important considerations were to make the device simple and affordable so that it would be easy to use both in the
shipping and on the road and low cost to make it accessible to all companies/organizations.
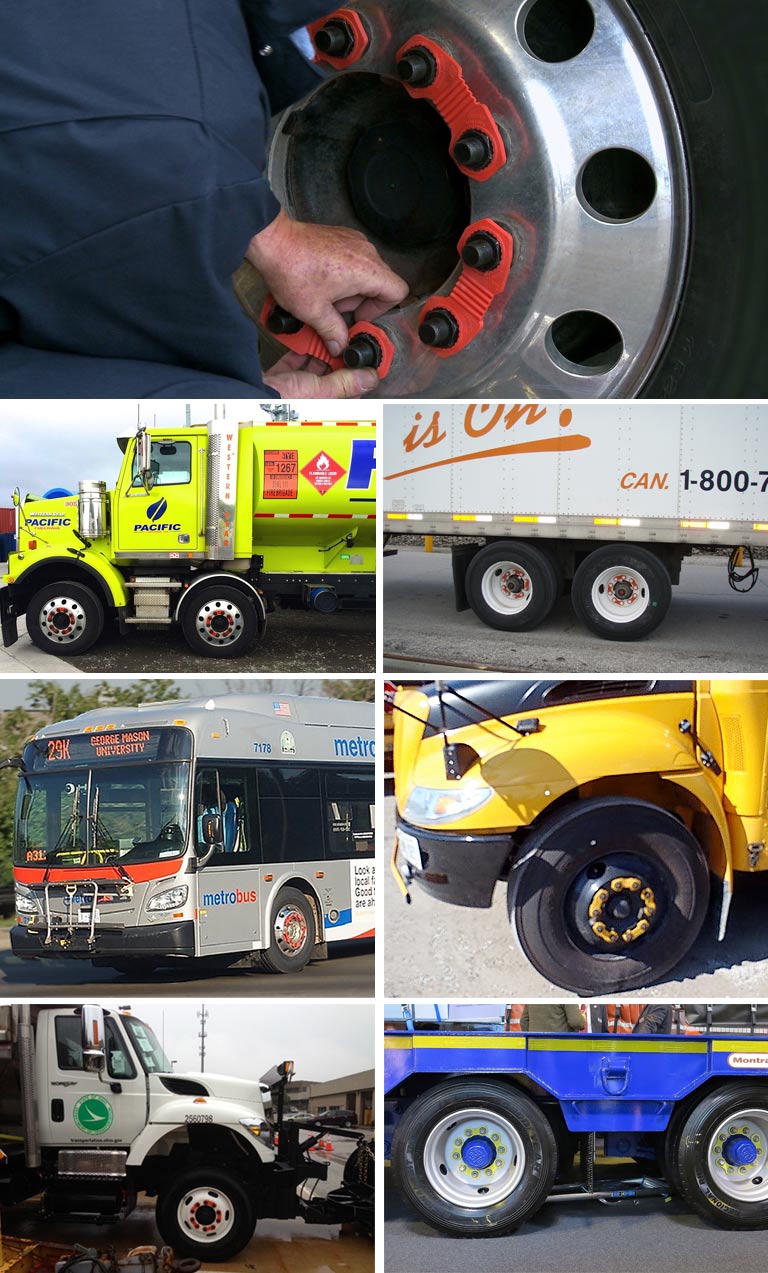
Tafcan and our Distributors are determined to increase the awareness that there is a solution to wheel nuts coming loose and how Zafety Lug Lock® can prevent wheel separations and wheel-end damage.
Proprietary Ownership
- Tafcan Consulting Ltd.
- All Trademarks and Patents are owned by Tafcan Consulting Ltd.
- Zafety Lug Lock® is a Patented Product (2014) and a Registered Trademark of Tafcan Consulting Limited.
- Manufactured in an ISO 9001:2008 facility in Ontario, Canada, North American sourced raw materials
Ifor (Taffy) Davies, President at Tafcan Consulting Ltd., is the inventor and manufacturer of Zafety Lug Lock®.
Taffy felt that it was important to focus on the largest vehicles first, as the accidents caused are costlier with damage, potential fines and lawsuits and often tragic with victim injuries and fatalities. Other important considerations were to make the device simple and affordable so that it would be easy to use both in the shipping and on the road and low cost to make it accessible to all companies/organizations.
Conception
While Ifor Davies (Taffy), of Tafcan Consulting Ltd., was in discussions with truck drivers, it became apparent that their attention and concerns focused on wheel safety and the fact that there was no satisfactory solution to assist the transportation industry with the reoccurring problem of wheel lug nuts loosening and falling off, causing wheel-off situations. Drivers were only aware of a product that indicated that the nut might be loosening, and at the time, no products that could retain the nuts. Taffy initiated a design process and after many iterations it became apparent that the most practical design would attach to two nuts. Taffy worked with a plastics engineer, to determine the most appropriate type of design-engineered plastic to meet all the requirements (listed below) and utilizing injection-molding technology.
Zafety Lug Lock® was in a continuous phase of development for 3 years. The goal was to develop a device that would lock the lug nuts and that would be superior to anything on the market today. The ultimate objective was to create a wheel nut retainer not just a wheel nut indicator. Listed below are the initial criteria and the device meets these specifications.
- A device that had sufficient strength to be installed on a lug nut and sufficient elastic retention to keep it in place under the tremendous Centrifugal forces that it would be subjected to on a spinning wheel rim.
- The device had to retain its strength and elasticity at temperatures of -40 degrees Centigrade (-40°F).
- The device had to be fully functional at transient temperatures as high as +120 degrees Centigrade (+248°F).
- The device had to retain its physical characteristics including color, properties and surface texture for at least 5 years.
- The device had to be highly visible.
- The device had to be reusable. The goal was to make the device so it could be installed it up to 10 times without impairment to the device.
- The device had to install manually with someone’s fingertips to ensure secondary tooling would not be required.
- The device had to have sufficient rigidity and tensile strength to prevent a lug nut from turning within it once it was installed.
- The device needed to be inert or resistant to the chemicals it might be exposed to in use and these included.
Road Salt | Liquid calcium chloride | Windshield washer alcohols | Radiator fluid |
Hydraulic fluid | Transmission fluid | Gasoline | Iron oxides |
Locktite | Diesel fuel | Ethanol alcohol |
Zafety Solutions do not have to be expensive or complex!
Temperature & Vibration Test
July 10, 2008
3.5” x 33mm standard temperature Zafety Lug Lock® Units
This report contains the results from the Temperature & Vibration tests performed on three (3) Zafety Lug Lock® Units for Tafcan Consulting Ltd. A representative from TAFCAN was present to install the Zafety Lug Lock® onto the lug nuts of the wheel prior to attachment onto the vibration platform. The vibration tests were performed on the vertical table of the Thermotron DS640 vibration test system.
Results: On completion of the vibration testing at 25 °C, a posttest visual inspection indicated that the Zafety Lug Lock® did not sustain any external damages or physical degradation and no evidence of any looseness. Again, upon completion of the vibration testing at each temperature level of +55 °C and -40 °C, a posttest visual inspection indicated that the Zafety Lug Lock® did not sustain any external damages or physical degradation and no evidence of any looseness of the lug nuts.
Temperature & Vibration Test
August 18, 2009
4-1/8” x 33mm standard temperature
Zafety Lug Lock® Units on steel and alloy rims.
This report contains the results from the Temperature & Vibration tests performed on Zafety Lug Lock® Units for Tafcan Consulting Ltd. Tafcan consulting Ltd. submitted two (2) wheel hubs for testing purposes – one 26″ Alloy Rim (Hub-Piloted Rim & Nuts) and one 26″ Steel Rim (Standard Nuts).
A TAFCAN representative was present to install the Zafety Lug Locks® onto the hand tightened lug nuts of the wheel prior to attachment to the vibration platform. All nuts were hand tightened. The vibration at temperature tests were performed on a vertical motion THERMOTRON DS-640 shaker table situated inside a THERMOTRON thermal chamber.
Results: Post-test visual inspections indicated the Zafety Lug Locks® did not sustain any external damages or physical degradation. Further, no looseness of any lug nuts was indicated.
Temperature & Vibration Test
October 14, 2009
4-1/8” x 33mm high temperature Zafety Lug Lock® Units.
This report contains the results from the Temperature & Vibration tests performed on Zafety Lug Lock® Units for Tafcan Consulting Ltd. A TAFCAN representative was present to install the Zafety Lug Locks® onto the hand tightened lug nuts of the wheel prior to attachment to the vibration platform. All nuts were hand tightened. The vibration at temperature tests were performed on a vertical motion THERMOTRON DS-640 shaker table situated inside a THERMOTRON thermal chamber.
Results: Post-test visual inspections indicated the Zafety Lug Locks® did not sustain any external damages or physical degradation. Based on the photographic documentation there was no evidence that any of the nuts had moved.
Durability Test
October 9, 2009
4-1/8” x 33mm high temperature Zafety Lug Lock® Units.
In order to complete this project, Tafcan provided Exova with twenty Zafety Lug Locks® to be installed on a 40-ft Transit Bus undergoing durability testing on Exova’s 6-Post Tire Coupled Road Simulator. Tafcan installed 5 Zafety Lug Locks® on each of the four wheels on the bus. The bus was then subjected to 207,906 simulated durability miles on the road simulator. Observations were recorded throughout testing.
Results: No issues were noted for the duration of the test.
Re-Torque Physical Test
October 25, 2010
3.5” x 33mm standard & 4-1/8” x 33mm high temperature Zafety Lug Lock® Units.
The objective of the proposed work was to provide information needed to evaluate the serviceability of the “Zafety Lug Lock®” samples when subjected to nut torque check and accidental nut torque with “Zafety Log Lock®” installed.
Results: No failure was observed during visual examination of the tested samples. No deformations of the entire unit were observed, all samples maintained the initial shape. No cracks or wear were observed on the tooth saw section (area in contact with the nut) on any tested samples.
Torque Test Report
June 25, 2009
3.5” x 33mm standard temperature Zafety Lug Lock® Units.
A series of tests were carried out on lug nuts with Zafety Lug Locks® installed to verify the torqued readings.
A technician from Topline Trailer Service Ltd. Performed the torque check on both alloy and steel rims.
Results: No evidence of movement.